Polymer injection molding is a vital manufacturing method that has changed the manner products are manufactured throughout different industries. This technique allows for the effective and accurate production of plastic components, serving to everything from vehicle components to consumer electronics. By grasping the details of plastic injection molding service , companies can enhance their manufacturing capabilities and realize innovative designs to life.
In today's accelerated market, the requirement for premium plastic parts is on the increase. The plastic injection molding service offers a adaptable solution that not only improves production tempo but also raises the general quality of the finished products. This piece will explore the principles of plastic injection molding, its advantages, and how mastering this art can lead to substantial progress in manufacturing methods.
Comprehending Polymer Injection Molding
Polymer injection molding is a extremely efficient production process used to create a wide range of plastic parts. It involves forcing liquid polymer into a form, in which it cools and sets into the intended shape. This process is preferred for its capability to produce complex designs and high precision parts, rendering it perfect for different industries including automotive, consumer goods, and electronic devices.
The process starts with the selection of the suitable polymer resin, that is then warmed to a liquid state. Once at the proper heat level, the liquid polymer is forced into a mold cavity under elevated pressure, allowing it to fill every detailed feature of the cast. After solidified, the mold opens, and the freshly created plastic part is removed. This process can be circle repeated multiple iterations, producing significant quantities of uniform parts in a comparatively brief duration.
A single of the important benefits of plastic injection forming is its adaptability. Whether a project needs small series production or large scale manufacturing, this method can accommodate varying degrees of volume and complexity. Additionally, with advancements in tech, there are ongoing enhancements in the substances and equipment used, improving efficiency and lowering expenses, ensuring that polymer injection molding remains a leading option for producers across the globe.
Benefits of Plastic Inject Molding Services
One of the main advantages of plastic inject forming services is the capability to manufacture large quantities of parts with uniform quality. This method allows producers to create complex shapes and forms that are uniform across large batches. The precision of the molds used ensures that each part is manufactured to specific specifications, significantly reducing the need for additional finishing or modification. This effectiveness not only optimizes production but also helps maintain tight tolerances that are critical in many uses.
Another advantage is the substance versatility offered by inject molding. A wide range of thermoplastics and thermosets materials can be utilized, allowing companies to choose materials that best fit their product requirements. This flexibility means that components can be designed with specific attributes such as strength, durability, or protection to chemicals and heat. Furthermore, with improvements in sustainability technology, using eco-friendly materials in polymer injection forming is becoming increasingly viable, aligning with corporate eco-consciousness goals.
Cost-effectiveness is a major benefit of using plastic injection forming services, especially for larger production runs. Although the upfront costs for producing molds can be high, the effectiveness of the process leads to lower per-unit costs when producing in bulk. Additionally, the speed of production means quicker turnaround times, allowing businesses to meet customer demands rapidly. Minimized waste and minimized labor costs also add to overall savings, making this method an appealing option for businesses looking to enhance their manufacturing processes.
Choosing the Ideal Injection Molding Partner
Selecting the right plastic injection molding service is vital for the achievement of your project. Begin by evaluating the provider's experience and expertise in the field. A partner with a proven history will grasp the details of plastic injection molding and be able to address individual needs successfully. Look for case studies or reviews that highlight their capability to manage assignments similar to yours.
Interaction is an additional essential aspect to take into account when choosing an injection molding partner. A collaborative approach can enhance the development procedure and help detect potential issues in advance. Consider their willingness to interact with you throughout the project, from the initial design phase to manufacturing. Open lines of communication will secure that your goals align and that the final product meets your requirements.
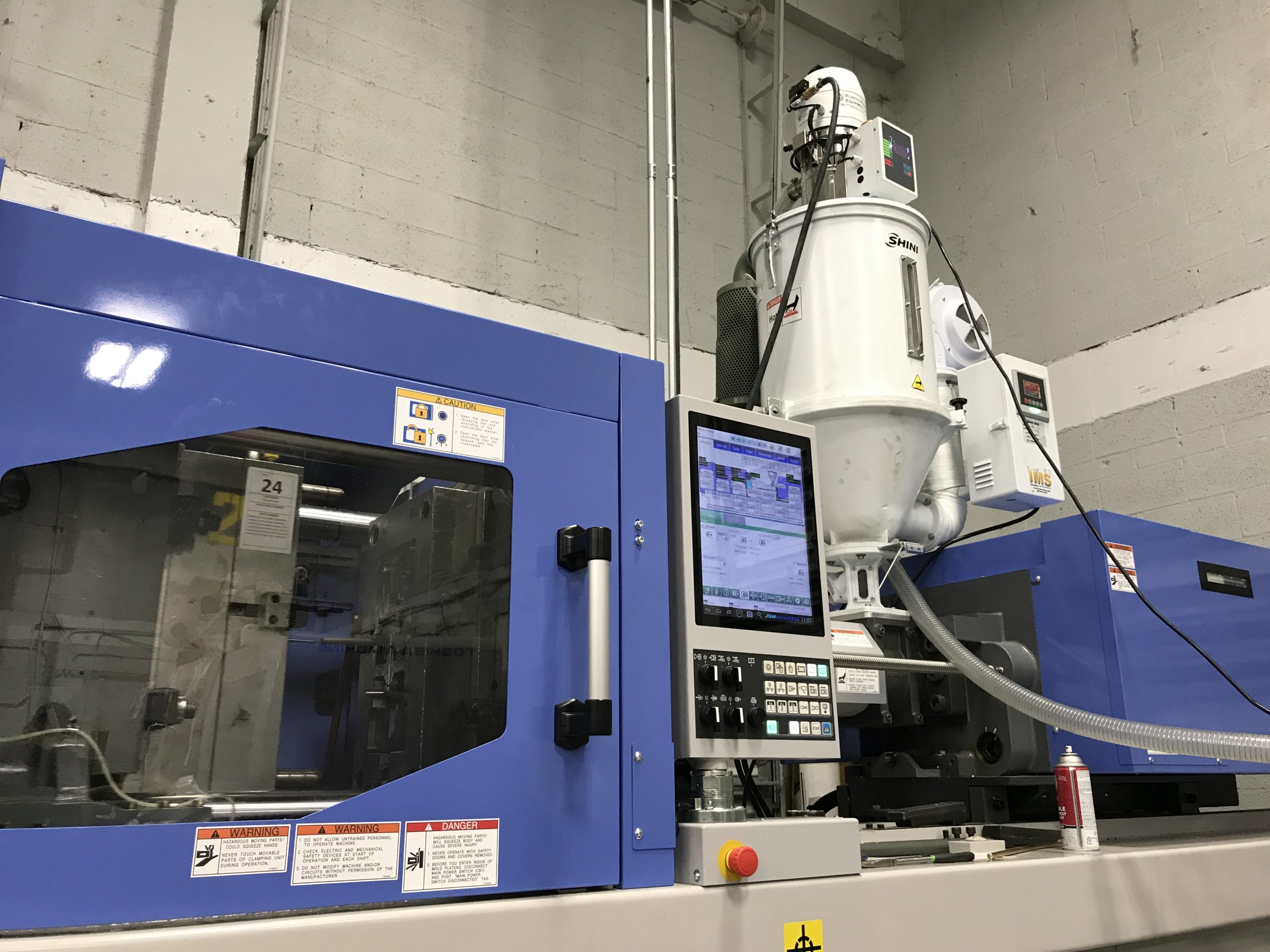
Finally, consider their production capacity and technology. A provider that invests in state-of-the-art equipment and innovative processes can deliver better quality and effectiveness. Ask about their quality control practices and their capabilities to scale production as requirements changes. By choosing a plastic injection molding provider that focuses on both quality and reliability, you establish the foundation for a successful partnership and a superior final product.